Why PAT Testing Is Important For Fire Safety
27th Mar 2017
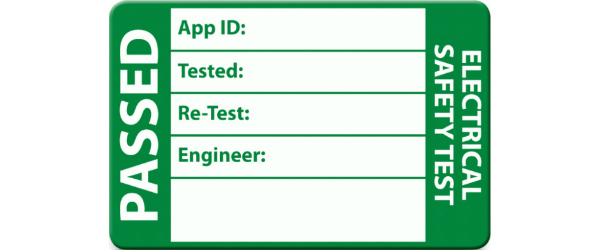
You may have heard the term PAT testing thrown around the workplace occasionally, but what is it? Why is it important and what does it have to do with fire safety?
What is PAT Testing
PAT testing means Portable Appliance TestingPAT testing means Portable Appliance Testing. It is the examination of electrical appliances and equipment to ensure that they are safe to use. This involves a visual inspection of the equipment, cables and plugs to ensure that they are in good condition, verification of grounding continuity and testing the soundness of insulation between current carrying parts. All of this combines to make the devices used within a business safe to use.
The Electricity at Work Regulations 1989 requires any and all electrical equipment, which has the potential to cause injury, to be maintained in a “safe condition”. However, the Regulations do not specify exactly what needs to be done to satisfy this requirement, how frequently, nor who by. So, it’s left to business owners and operators to satisfy the requirement to the best of their ability. This is where formal PAT inspection comes in. It’s not required by law, but a good way of satisfying the regulations that are in place.
Why PAT Is Important For Fire Safety
In the year 2014-15 in England, over 12% of domestic house fires were caused by electrical appliances. Yet, most businesses arguably contain more electronics, which are often more regularly and vigorously used.
PAT inspection ensures that all “portable” electronics in the business are safe for use by the business. “Portable”, in this respect, is a little misleading but is generally regarded as anything that gets plugged into a wall socket. PAT ensures that these portable appliances are safe for the business to use. It ensures that there’s little chance of accidental injury due to faulty electronics, reducing the risk to the user and other business personnel. It also ensures that there’s less risk of more substantial damage to electrical equipment, which can involve repair or replacement costs and business downtime. Finally, it ensures that there’s little chance of an electrical fire starting due to faulty or overloaded equipment.
Don’t let PAT testing make your employees complacent
Just because devices have been checked and certified, doesn’t mean that absolutely nothing can go wrong with your electrical equipment. Sockets can still become overloaded and faulty equipment can still overheat. Sockets can still become overloaded and faulty equipment can still overheat
If an ‘in office ’laptop’ that never leaves the desk gets transitioned into a travel laptop that moves around a lot, the charger and device will need to have a more frequent visual and PAT inspection to account for the more rigorous wear and tear.
Don’t allow employees to become complacent and take the safety of their devices for granted. Ensure that employees are correctly educated in proper Portable Appliance safety and teach them to recognise the early warning signs of a dangerous cable, faulty port or failing socket. When it comes to personnel safety and fire safety, an ounce of prevention is worth a ton of cure.
However if you follow the timetable (usually annual) for when PAT should be carried out again under normal use conditions, you can operate with a lot more peace of mind.
PAT inspections and testing are just a small part of wider fire safety procedures that your business should be implementing. The regularity of PAT should be clearly outlined in your Fire Risk Assessment and should form part of your business’s regular safety duties alongside fire alarm testing and drills, visual electronics inspection, fire extinguisher testing and maintenance etc.